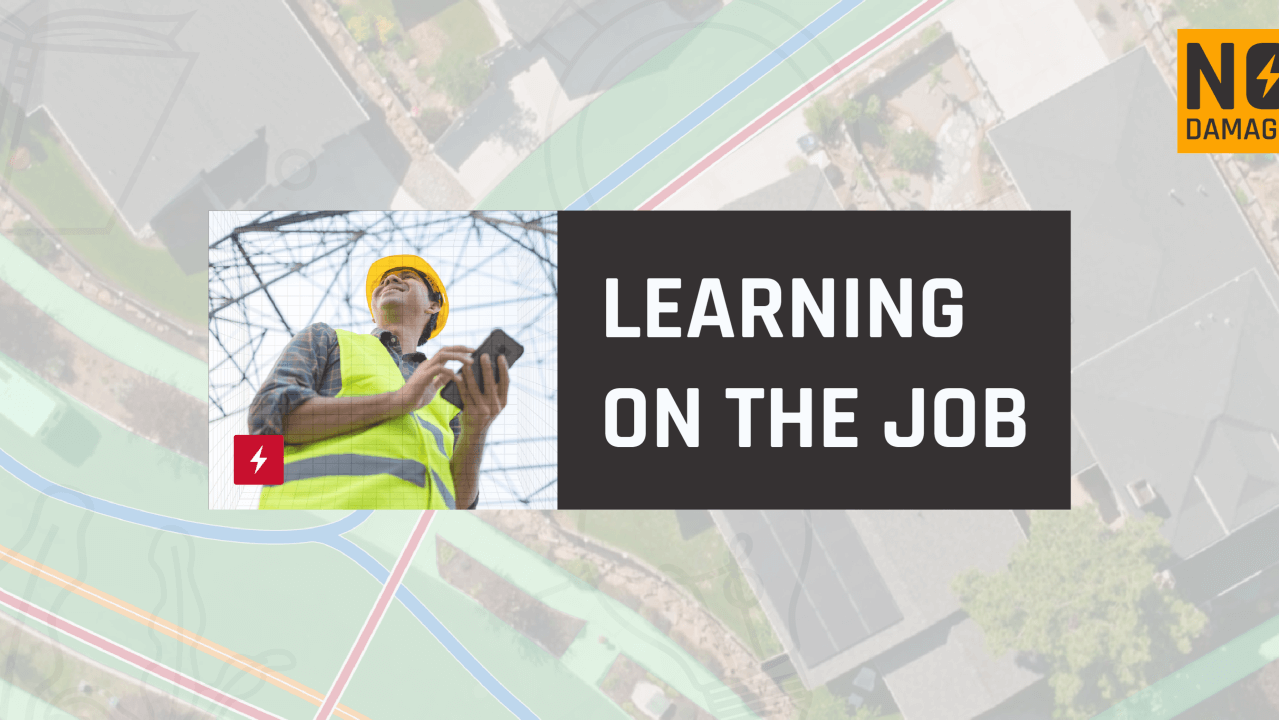
The ability to prevent damage to underground infrastructure hinges on both technical expertise and practical experience. On-the-job learning plays an indispensable role in bridging the gap between formal training and real-world application. Locators who engage in continuous learning on the job are better equipped to navigate the specific challenges of their work environment, such as identifying subtle variations in soil conditions, interpreting complex locate tickets, and using detection equipment effectively under varying conditions.
While this piece emphasizes the value of on-the-job learning, it’s important to clarify that this is not an endorsement of placing unqualified or untrained individuals in roles they are not prepared to handle. Instead, the focus is on refining the skills of already qualified locators, ensuring they continuously improve and adhere to the highest standards—often exceeding legal requirements.
One of the most common hurdles in any field is the emphasis on years of experience when hiring for critical roles. Granted some locate jobs don't require too much experience but I think in order to retain staff and help them gain years worth of experience we need do something! This is where a structured approach to on-the-job learning becomes invaluable. By implementing strategies that allow new locators to gain experience quickly and effectively, companies can bridge this gap, cultivating a skilled workforce ready to meet the demands of damage prevention.
Research consistently underscores the value of on-the-job learning in enhancing employee performance and adaptability. Studies show that experiential learning—gaining knowledge through direct experience—significantly improves an individual’s ability to apply concepts in practical situations, especially in fields requiring high levels of technical skill and situational awareness.
From my own experience, learning on the job has been instrumental in mastering the processes my we prioritize. This kind of learning is particularly effective when a company is committed to setting up its employees for success. When an organization is dedicated to its damage prevention protocols, provides the right tools, and fosters an environment where continuous learning is encouraged, employees are more likely to develop the skills necessary to perform their roles to the highest standards.
UPSKILLING
For companies to fully harness the benefits of on-the-job learning in damage prevention, they must create a supportive environment that encourages continuous improvement. Here’s a mini-plan to help new locators gain experience quickly and effectively:
- Structured Onboarding Program: Develop a comprehensive onboarding program that pairs new locators with experienced mentors from day one. This program should include a mix of classroom instruction on the fundamentals of utility locating, shadowing experienced locators in the field, and gradually taking on more responsibility under supervision.
- Hands-On Training Modules: Create a series of hands-on training modules that simulate common challenges faced in the field. These modules can include mock locate scenarios, equipment handling exercises, and problem-solving tasks designed to build confidence and competence. The focus should be on practical skills that new locators can apply immediately.
- Progressive Responsibility: Implement a phased approach where new locators start with less complex tasks and gradually take on more challenging assignments as they demonstrate proficiency. This allows them to build experience incrementally, reducing the risk of errors while they are still learning.
- Regular Feedback and Evaluation: Establish a system of regular feedback and evaluation, where new locators receive constructive input on their performance. This feedback loop should include specific areas for improvement as well as recognition of their progress. Regular check-ins with mentors and supervisors ensure that new locators are on track and receiving the support they need.
- Encouragement of Curiosity and Innovation: Encourage new locators to ask questions, explore new techniques, and share their observations. A culture that values curiosity and innovation reduces the fear of making mistakes and empowers employees to take initiative. This can be fostered through regular team meetings where locators discuss challenges and share solutions.
- Debriefing Sessions: After each day or week, conduct debriefing sessions where the team reviews what went well and what could be improved. These sessions are crucial for reinforcing lessons learned and helping new locators understand the broader impact of their work on damage prevention efforts.
- Recognition and Rewards: Recognize new locators who demonstrate rapid learning and contribute positively to the team. Whether through public acknowledgment, bonuses, or advancement opportunities, recognition motivates continued growth and sets a standard for others to follow.
ORGANIZING
On-the-job learning is a powerful tool that can transform skilled locators into experts who consistently deliver high-quality results. However, this only works effectively when a company is genuinely invested in its employees' success. Organizations must provide the necessary resources, foster a culture of continuous learning, and set clear expectations that go beyond basic legal compliance. When locators are supported in this way, they are better prepared to handle the complexities of their roles, ultimately leading to fewer damages, safer work environments, and a more resilient infrastructure network.
In conclusion, while formal training provides the foundational knowledge required for utility locating, true mastery comes through learning on the job. Companies that prioritize and support this continuous learning process will not only enhance the skills of their employees but also drive the overall success and safety of their operations. By implementing structured programs that help new locators gain experience quickly, organizations can ensure they are building a workforce capable of meeting the highest standards in damage prevention.
Share this Post