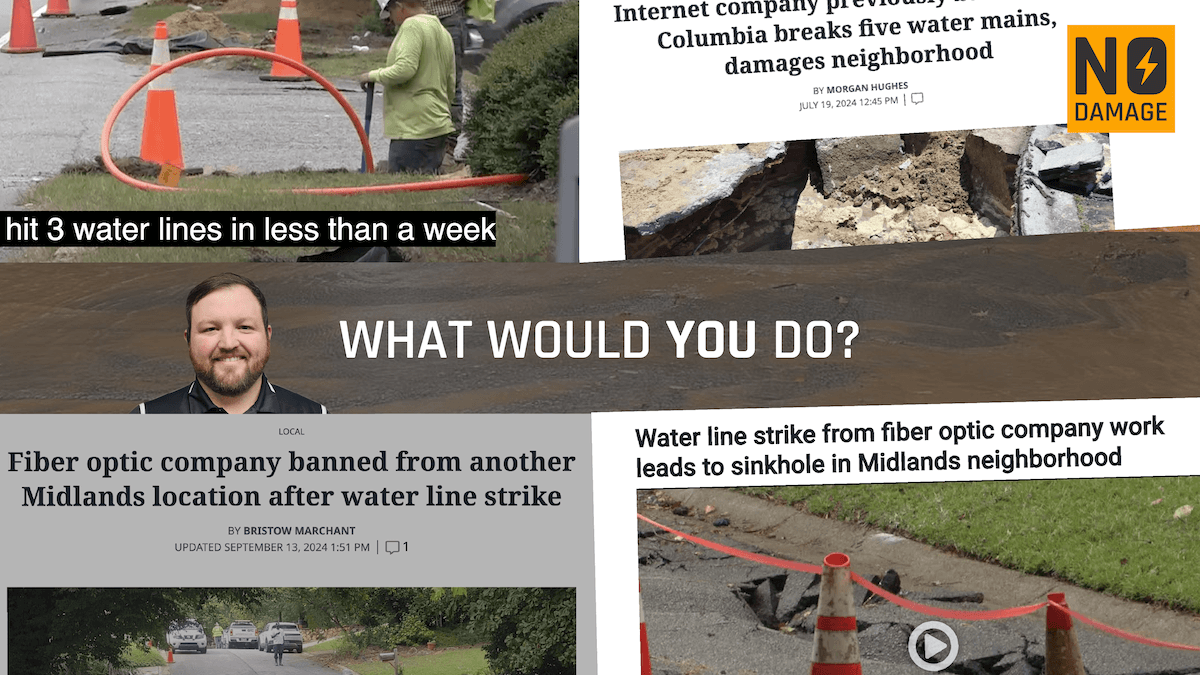
I recently came across this article about Lumos Fiber being banned from digging in a community due to repeated utility strikes and damage. As I read through it, I couldn’t help but wonder - what would I do if I were in that company’s shoes? How would I respond to being banned from working in an area because of damage to critical infrastructure?
The situation immediately made me think about the core of the issue: safety, oversight, and culture. If I were leading a company in a similar position, my first priority would be an internal investigation to identify where things went wrong. Were utility lines properly marked? Were locate tickets mishandled? Did the crews lack proper training or fail to follow protocols? Did we provide them the tools to do the job? Are our targets forcing unsafe behavior? An honest and frank internal review would be the foundation of rebuilding and preventing further incidents. Just like we conduct damage investigations, we need to review and audit every single thing contributing to our internal problems. But that’s only the beginning.
A Culture of Safety Starts from the Top
One of the most pressing issues in any scenario like this is safety culture. It’s easy to point fingers or find scapegoats when things go wrong, but real leadership means acknowledging that if safety failures are happening repeatedly, the problem runs deep. As the head of such a company, I’d start with the question: What are we prioritizing? Too often, rapid expansion or project deadlines overshadow the need to put safety first. If I were in charge, I would recalibrate the entire organization to focus on safety as the primary priority, above everything else. This means every single person, from management to field crews, would undergo regular training, not just as a formality but as a fundamental part of how we operate. The ROI on safety is clear, so when confronted by investors or the board worried about the bottom dollar I'd assure them that this direction will ensure long term success. Plus whatever is going on right now is NOT working!
The other dimension to this is; culture trickles down through the company. There might be some staff who refuse to adapt to our new safety prerogative and we'd have to make that adjustment - there's no room for people not concerned about safety or damage prevention. But we'll start at the top and work our way down.
Proactive, Not Reactive
The article made it clear that the company in question faced issues because they failed to be proactive about risk management. If I were leading a company, I’d make proactive measures the cornerstone of our strategy. We would no longer simply respond to issues as they arise but instead work to prevent them from happening in the first place. This could mean requiring every project to go through an enhanced risk assessment process before a single shovel hits the ground. Pre-dig inspections, smarter use of locate technology, and leveraging existing tools like GIS mapping would be key. SHANE HART wrote last week about utility surveys being a proactive measure we can all take. That seems like a no-brainer.
One step we could take is introducing real-time communication between field crews and utility providers using integrated ticket management systems like Utilocate . This would ensure that everyone involved has up-to-date information and that any discrepancies in utility markings or locate tickets are addressed immediately.
Internal Investigations and Accountability
Alongside cultural shifts and technological upgrades, I’d conduct thorough internal investigations for each and every utility strike. No incident should be swept under the rug. A dedicated team would analyze what went wrong and why. Was it an issue with training, equipment, or miscommunication? Once the root cause is identified, we’d not only fix that particular problem but put systems in place to prevent similar incidents in the future.
In parallel, accountability would become a central tenet. If I were running the company, I would hold both management and field teams accountable for any preventable damage. That’s not to say we’d create a culture of blame, but instead, one of responsibility. Field teams should feel empowered to report near-misses or unsafe conditions without fear of retribution, knowing that this information is critical to our safety improvements.
Leveraging Technology to Prevent Future Incidents
Technology plays a huge role in damage prevention, and I’d ensure that we were making the best use of every tool available. Using locate wands, augmented reality overlays, and enhanced AI systems would give field workers the clearest possible picture of what lies beneath the surface before they start digging. Advanced ticket management systems would be mandatory for tracking every single step of the process, from planning to post-job audits.
One of the biggest mistakes companies make is underestimating the data they already have. If I were leading a company in this situation, I’d ensure that we were leveraging all of our available data—using it to predict risks, identify trouble spots before they escalate, and proactively plan around known issues. The power of AI and predictive analytics can help us foresee problems and reroute crews to prevent damage, saving time, money, and public trust.
Transforming Relationships with Local Authorities
Rebuilding trust with local governments and utility companies would be essential if we were to move forward. I’d ensure we worked closely with public works departments, sharing our data, findings from our internal investigations, and most importantly, our plan for preventing future damage. Open lines of communication are essential. That means more than just waiting for approvals—it means being transparent about the changes we’re making and demonstrating that we’re serious about doing things differently.
Prioritizing Continuous Training and Education
If we expect field crews to dig safely, we need to give them the right tools and training. Safety training would become a continuous process, rather than a one-time requirement. Field crews would be equipped with not only the best physical tools for the job but also real-time access to utility data and an understanding of how to use it effectively. It’s not enough to say, "Mark and dig carefully"; teams need to be trained in the nuances of using technology like GPS, locate wands, and augmented reality. I'd also like to make sure that our staff have the opportunity to get trained in disciplines they're not necessarily practicing like locate certification for drillers. I think there's a lot of opportunities for cross pollination between field roles that could benefit our safety goals.
We’d also encourage field teams to take part in post-incident reviews, learning from every mistake so that the same issue never occurs twice. This would be paired with ongoing workshops and scenario-based training, reinforcing how to handle complex digs where multiple utilities overlap.
From Reactive to Proactive: Building a Legacy of Safety
If I were running a company that had been banned due to damage incidents, my long-term goal would be to move the organization from a reactive to a proactive mindset. I’d want our name to be synonymous with safety, precision, and reliability, turning our setbacks into the groundwork for becoming a leader in damage prevention.
Our focus would be on long-term cultural change, driven by continuous education, accountability, and the use of advanced technology to not just prevent damage but to ensure we are always a step ahead. In time, I’d want the communities we serve to see us as a company that not only delivers on its promises but one that truly cares about their safety and well-being.
If you don’t take this approach after being banned from digging, you’re not just risking your next project - you’re putting your entire company’s future at stake.
Share this Post